Feldstudie 2.0 zur Modul- und Anlagenqualität auf Basis thermografischer Messungen von 1 GW
Bernhard Weinreich, Björn Schauer, Simon Gürzing, Rudolf Haas
HaWe Engineering GmbH, Mühlthaler Weg 1, 82131 Gauting-Hausen
Tel.: 089/740 433-13, weinreich@hawe-eng.com, www.hawe-eng.com
HaWe Engineering GmbH, Mühlthaler Weg 1, 82131 Gauting-Hausen
Tel.: 089/740 433-13, weinreich@hawe-eng.com, www.hawe-eng.com
1. Motivation, Ziele und Hintergrund
Auch wenn die deutsche Energiewende in den letzten Jahren ins Stocken geraten ist und dafür in anderen Ländern Fahrt aufnimmt, so sitzt Deutschland in Bezug auf die Photovoltaik immer noch auf einem großen Erfahrungsschatz. Dieser manifestiert sich nicht zuletzt im Betrieb eines Anlagenbestands von 46 GW [ISE1]. Dessen Besonderheit ist, noch vor seiner Größe, sein mittleres Alter von bereits 8 Jahren. Ein wichtiger Teil der sich aus dem Betrieb ergebenden Erfahrungen ist das Wissen um die Art erwartbarer Fehler, deren Häufung und dem effizienten Umgang im Sinne einer wirtschaftlichen Behebung und somit effizienten Betriebsführung.
1.1 Ziel und Übersicht zum Inhalt
Ziel der vorliegenden Feldstudie 2.0 ist es, einen Teil des Wissens um die Häufungen thermografisch auffindbarer Anlagenfehler zu heben und zugänglich zu machen. Wie die erste Feldstudie von 2013 [SolS] gewinnt auch die Neuauflage ihre Daten aus eigenen Thermografie Gutachten der letzten Jahre. Die Werte setzen sich aus 420 Einzelmessungen in PV Anlagen (PVA) mit insgesamt knapp 1 GW zusammen. Hierin enthalten sind auch die 41 Messungen aus der ersten Feldstudie. Neben dem Umfang erweitert sich die neue Studie zusätzlich um Auswertungen von Dünnschicht (DS) Generatoren und die PV-Elektro-Thermografie an GAKs, ACHVs¹ und Wechselrichtern (WR). Auch sind erstmals zeitliche Entwicklungen dargestellt, sowohl entlang der Anlagengenerationen als auch über die Komponentenalterung und ein Blick auf die Wirtschaftlichkeit der Thermografie selbst.
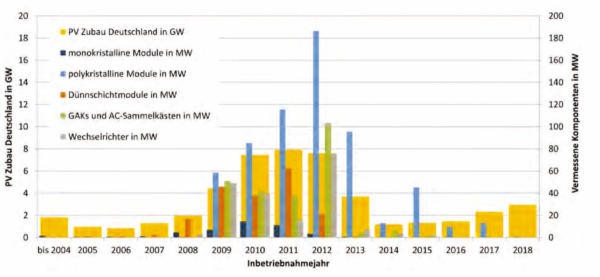
Abbildung 1: Überlagerung der Leistungen, des deutschen PV Zubaus [ISE] durch fünf Vermessungs-/ Komponentenkategorien, im Verhältnis 100:1 über die Inbetriebnahme Jahre.
1.2 Rahmen der Datenbasis
Seit 2009 hat die Solarschmiede GmbH und ab 2014 der fachtechnische Nachfolger HaWe Engineering GmbH 237 PV-Anlagen der Größen 0,1 - 50 MW thermografisch vermessen. Die Analysen der Anlagen aus 1997 - 2018, mit insgesamt 962 MW, sind nach den folgenden Hauptbaugruppen unterteilt und anteilig vermessen:
- PV-Thermografie der Generatoren; Mittlere Stichprobe 90% => 866 MW
- Elektro-Thermografie von GAKs, WR, ACHVs; Stichpr. 20% => 193 MW
- Elektro-Thermografie von GAKs, WR, ACHVs; Stichpr. 20% => 193 MW
In 24 Anlagen mit zusammen 202 MW fanden 2 - 6 fache Mehrfachmessungen statt, die für das Verständnis von Fehlerentwicklungen sehr erkenntnisreich waren.
Mit 848 MW lag 88 % der vermessenen Leistung in Deutschland, der Rest vornehmlich innerhalb Europas. Damit wurden knapp 4 % der hiesigen Großanlagen
> 0,1 MW untersucht, die mit etwa 22 GW [ISE2] knapp die Hälfte der deutschen PV-Leistung ausmachen.
Über 95% der Messungen, und damit auch ein Großteil aus den frühen Jahren, entsprachen den Anforderungen der aktuellen IEC TS 62446-3:2017² [IEC]. Stark in der geometrischen Auflösung reduzierte Überflüge mittels Drohne, blieben in der Feldstudie gänzlich unberücksichtigt. Alle Messungen und damit auch die 29 detaillierten, radiometrischen Drohnen-Befliegungen von 45 MW, waren immer von umfangreichen visuellen Inspektionen der Anlagen flankiert. Diese sind wesentlich für die Beurteilung vieler Befunde und die Sachverständigenarbeit. Ein großer Teil der Prüfungen fand im Rahmen von Abnahme und Gewährleistungsgutachten und ähnlich intensiven Analysen zu Anlagenperformance statt. Entsprechend standen häufig weitere Vergleichsdaten aus den Anlagen-Überwachungen, Kennlinien- messungen und weiteren Messungen zur Verfügung.
Mit 848 MW lag 88 % der vermessenen Leistung in Deutschland, der Rest vornehmlich innerhalb Europas. Damit wurden knapp 4 % der hiesigen Großanlagen
> 0,1 MW untersucht, die mit etwa 22 GW [ISE2] knapp die Hälfte der deutschen PV-Leistung ausmachen.
Über 95% der Messungen, und damit auch ein Großteil aus den frühen Jahren, entsprachen den Anforderungen der aktuellen IEC TS 62446-3:2017² [IEC]. Stark in der geometrischen Auflösung reduzierte Überflüge mittels Drohne, blieben in der Feldstudie gänzlich unberücksichtigt. Alle Messungen und damit auch die 29 detaillierten, radiometrischen Drohnen-Befliegungen von 45 MW, waren immer von umfangreichen visuellen Inspektionen der Anlagen flankiert. Diese sind wesentlich für die Beurteilung vieler Befunde und die Sachverständigenarbeit. Ein großer Teil der Prüfungen fand im Rahmen von Abnahme und Gewährleistungsgutachten und ähnlich intensiven Analysen zu Anlagenperformance statt. Entsprechend standen häufig weitere Vergleichsdaten aus den Anlagen-Überwachungen, Kennlinien- messungen und weiteren Messungen zur Verfügung.
1.3 Abgrenzungen zu unberücksichtigten Auffälligkeiten
Die statistischen Auswertungen sind um die folgenden drei Kategorien bereinigt:
1.3.1 Bereits vor Untersuchungen bekannte Befunde
Im Sinne der Homogenität der Daten ohne Ausreißer durch vorab bekannte Großschäden sind die Analysen um Ergebnisse aus Schadensgutachten bereinigt. Hierzu zählen beispielsweise thermografischen Untersuchungen im Rahmen von Blitz-, Hagel- und Sturmereignissen, so wie großflächig, erwartete Modulserienfehler. Vorab bekannt und erwartbare Schäden, die sich mittels Thermografie konkretisieren ließen, sind vereinzelt gesondert dargestellt.
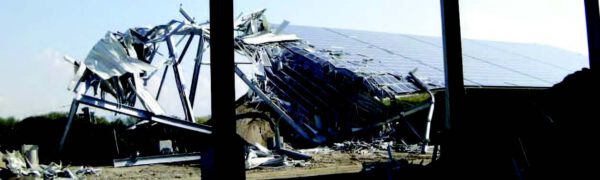
Abbildung 2: Eine der mehrfach thermografierten Anlagen, aus einem Sturmschadens- Gutachten. 0ie vorab leicht erkennbaren Modulschäden bleiben in der Studie unberücksichtigt.
1.3.2 Nicht thermografische Befunde
Weiter unberücksichtigt sind alle Auffälligkeiten, die rein visuell oder auf anderen messtechnischen Wegen erfasst wurden und die nicht im weiteren Kontext zur thermografischen Untersuchung stehen, hierzu zählen beispielsweise:
- Mechanische Auffälligkeiten wie niedrige Anzugsmomente
- Homogen niedrigere Modulleistung durch fehlerhafte Label oder Degradatio
- Homogen niedrigere Modulleistung durch fehlerhafte Label oder Degradatio
1.3.3 Auffälligkeiten aus nur einer Anlage
Befunde aus der thermografischen Untersuchung, die nur selten bzw. nur in je einer Anlage feststellbar waren, blieben ebenfalls außen vor, wie beispielsweise:
- PV-Thermografie: Fehlende Gummiauflagen zwischen Modul und Gestell
- Elektro-Thermografie: Erwärmte Erdleitung / Fehlerstrom auf Erdung
- Elektro-Thermografie: Erwärmte Erdleitung / Fehlerstrom auf Erdung
Auch diese Themen werden zum Teil gesondert diskutiert.
1.4 Thermografie als Basis der Studie
Die Thermografie von PV Generatoren und den elektrischen BOS³ Komponenten hat sich in den letzten Jahren bei vielen Betreibern und Betriebsführern als Mittel zur Qualitätssicherung etabliert. Dies gilt nicht nur für Einzelmessung im Rahmen von Abnahmen und Gewährleistungsgutachten, sondern immer häufiger auch für regelmäßige Kontrollen, zumindest in Form größerer Stichproben (10-50%).
Die Thermografie ist besonders geeignet für umfangreiche Untersuchungen des aktiven IST-Zustands einer Anlage. Zum einen erfasst sie in kurzer Zeit sämtliche einsehbaren elektrischen Verbinder und deren Übergangswiderstände, aber gleichzeitig auch das elektrische Betriebsverhalten bis auf den Arbeitspunkt jeder einzelnen Zelle. So können Betriebsabweichungen wie kurze WR-Stillstände oder System bedingtes Mismatch⁴ erfasst werden, die bei anderen Analysen durchs Raster fallen.
Die Thermografie ist besonders geeignet für umfangreiche Untersuchungen des aktiven IST-Zustands einer Anlage. Zum einen erfasst sie in kurzer Zeit sämtliche einsehbaren elektrischen Verbinder und deren Übergangswiderstände, aber gleichzeitig auch das elektrische Betriebsverhalten bis auf den Arbeitspunkt jeder einzelnen Zelle. So können Betriebsabweichungen wie kurze WR-Stillstände oder System bedingtes Mismatch⁴ erfasst werden, die bei anderen Analysen durchs Raster fallen.
1.5 Begriffsdifferenzierung PV- und PV-Elektro-Thermografie
Zum Oberbegriff Elektro-Thermografie, hat sich mit der 0IN V0E V 0126-23-3 (Ed. 1: 16/03)⁵ [DKE], der Begriff der PV-Thermografie gesellt, der sich auf die Aufnahme von PV Modulen bezieht. Diese beiden Begriffe werden hier, und voraussichtlich zukünftig auch in der Überarbeitung der IEC 62446-3, um den Begriff: PV-Elektro- Thermografie (PV-El-Th) ergänzt. Dieser benennt alle Prüfungen elektrischer Komponenten zwischen PV Modul und Mittelspannungs-Transformator. Im Kontext ebenfalls verwendet wird der Begriff: elektrische Balance of System (BOS) Komponenten, hierzu zählen:
- 0C seitig: Anschlussdosen, Steckerkupplungen, GAKs und WR-seitige Sicherungen und Trennschalter
- AC seitig: Wechselrichter mit Leistungsteilen, AC-Sammler, Sicherungen und Trennschalter.
- AC seitig: Wechselrichter mit Leistungsteilen, AC-Sammler, Sicherungen und Trennschalter.
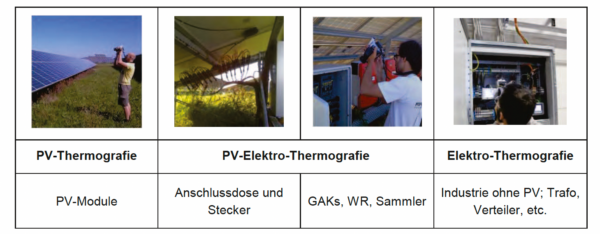
Sofern in der Anlage wie üblich eine größere Stichprobe am PV-Generator stattfand, wurden Auffälligkeiten aus der Generator-Messung wie beispielsweise Modulstrings im Leerlauf nicht erneut, doppelt bei der Auswertung der GAKs als beispielsweise ausgelöste Strangsicherung aufgeführt.
2. Statistische Auswertung der Felddaten
Im Folgenden wird der größte Teil der statistisch auswertbaren Auffälligkeiten aus der PV- und PV-Elektro-Thermografie vorgestellt und Einzelbefunde hervorgehoben.
2.1 Verwendete Bewertungs-Systeme
Die Klassifizierung von Befunden in Gutachten zu elektrischen BOS Komponenten folgte der VATh-Richtlinie zur Elektrothermografie⁶, die ihrerseits der DIN EN 54191⁷ folgt, wobei die VATh-Richtlinie die mittlere der hier dreistufigen Bewertung zu thermischen Auffälligkeiten (tA) in die zwei Kategorien Gruppe 2 und 3 aufspaltet:
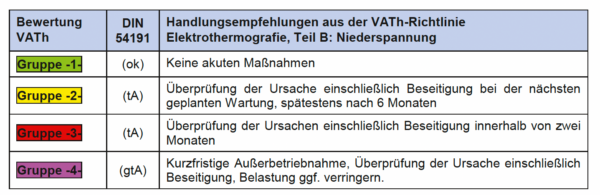
Die Bewertung der Module stellt eine firmeninterne Kategorisierung dar, die ihrerseits der VATh-Richtlinie folgt, dabei die mittleren beiden Kategorien aber noch weiter aufspaltet, abhängig davon, ob ein Komponententausch erforderlich ist:
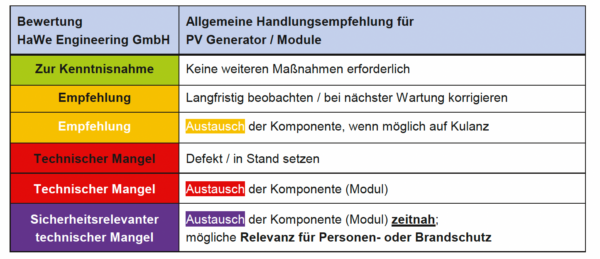
2.2 Auffälligkeiten im PV-Generator
PV-Generatoren sind in der Auswertung in Dünnschicht und kristalline Generatoren unterteilt, da sich beide in der Art typischer Fehler deutlich unterscheiden.
2.2.1 Modulmängel in kristallinen Generatoren
Innerhalb der 185 kristallinen Anlagen wird im Folgenden nicht weiter zwischen den 43 MW monokristallinen und 659 MW polykristallinen Modulen bzw. Generatoren unterschieden. Die relevantesten Unterschiede lagen im mittleren Inbetriebnahme Zeitpunkt von Anfang 2010 bei monokristallin und Mitte 2012 bei polykristallinen Anlagen und einem bei letzterem 1,5 fach höheren Anteil auffälliger Zellen, meist durch Zellbruch.
Für die folgenden Betrachtungen wurde zwischen drei Generationen für das Inbetriebnahmedatum differenziert: Die Anfangs- und Boomjahre in Deutschland, die beiden Jahre mit stagnierendem, aber hohem Zubau und die Jahre danach.
Für die folgenden Betrachtungen wurde zwischen drei Generationen für das Inbetriebnahmedatum differenziert: Die Anfangs- und Boomjahre in Deutschland, die beiden Jahre mit stagnierendem, aber hohem Zubau und die Jahre danach.
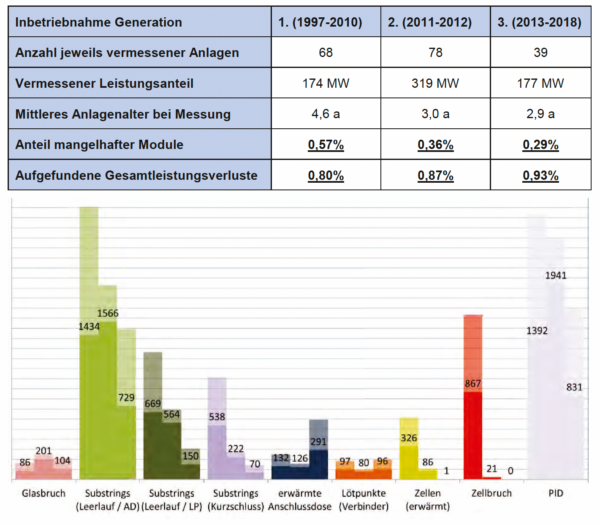
Abbildung 3: Absolute Zahlen Modulmängel / Generation und relative Häufung im Hintergrund
Bewertung der Modulfehler und deren Verteilung über die Generationen
Von erster zu letzter Generation zeigt sich in der Tabelle eine Halbierung der als mangelhaft bewerteten Module von 0,57% auf 0,29%. Bei der Betrachtung aller Auffälligkeiten ist zu berücksichtigen, dass stets ein Zusammenhang zwischen Anlagengeneration und Alter der Anlage zum Vermessungszeitpunkt besteht, wie auch in der vorausgegangenen Tabelle als Mittelwert angegeben.
Eine Trennung von Generation und Alterung ist bei der bisheriger Datenbasis noch schwierig, da zum einen jede Fehlerart unterschiedliche Alterungsgeschwindigkeiten zeigt und selbst innerhalb einer Fehlerart bisher sowohl abflachende als auch progressiv steigende Neufehlerzunahmen zum gleichen Thema und in ähnlichen Zeitskalen zu beobachten sind. Da solche Mehrfachmessungen zu einzelnen Themen nur einen kleinen Anlagenbestand zeigen, wären Aussagen hieraus noch nicht tragfähig, weshalb sie, wenn nur als Einzelmessungen dargestellt sind.
Die Glasbrüche zeigen im Verlauf über die Generationen keine besondere Veränderung. Der Ausreiser in der mittleren Generation wird als primär statistische Überhöhung gesehen, da sich 4 der 3 am stärksten betroffenen Anlagen in diesem Zeitabschnitt befinden, die allein etwas über 50% der Glasbrüche stellen.
Die beiden Arten von Substrings im Leerlauf (verursacht durch AD oder LP) zeigen einen kontinuierlichen Trend zur Abnahme. Dieser wird im Kontext einer steigenden Qualität bei der Herstellung der elektrischen Klemm- und Lötverbindungen gesehen.
Die Substrings im Kurzschluss sind um Anlagen mit lokalen Häufungen entsprechend Blitzeinschlägen bereinigt. Die dargestellt übrigen, werden hauptsächlich auf spontanes Versagen der Dioden zurückgeführt, das sich durch bessere Bauteilqualitäten und Auslegungen kontinuierlich gebessert haben kann.
Die unerwartete Steigerung der mangelhaften Anschlussdosen (AD) in der letzten Generation geht mit 2/3 der Gesamtmenge allein auf 2 Anlagen aus 2013 mit einem identischen Anschlussdosentyp zurück und hat daher im zeitlichen Verlauf keine Aussage. Ohne diese Dosen-Thematik ergäbe sich ein leicht fallender Trend.
Die Häufung mangelhaft ausgeführter Lötpunkte (LP) an Quer- und Zellverbinder zeigt, trotz einer flächigen Umstellung auf Lötautomaten, keinen klaren Trend. Die Anzahl betroffener Anlagen mit nur 13 mit je mehr als 5 Mängeln, ist hierfür zu klein.
Die Aufteilung Zellen „erwärmt" mit nicht eindeutiger Ursache und Zellbruch wurde aus der alten Studie übernommen, beide Verläufe zeigen klar, dass die Branche das Thema Zellbruch seit etwa 2012 überwunden hat.
Nach Inbetriebnahme 2013 ist nur noch eine als bedingt relevante bzw. als Empfehlung bewertete PID Anlage aufgefallen. Das Thema ist im Weiteren noch detaillierter aufgeschlüsselt.
Von erster zu letzter Generation zeigt sich in der Tabelle eine Halbierung der als mangelhaft bewerteten Module von 0,57% auf 0,29%. Bei der Betrachtung aller Auffälligkeiten ist zu berücksichtigen, dass stets ein Zusammenhang zwischen Anlagengeneration und Alter der Anlage zum Vermessungszeitpunkt besteht, wie auch in der vorausgegangenen Tabelle als Mittelwert angegeben.
Eine Trennung von Generation und Alterung ist bei der bisheriger Datenbasis noch schwierig, da zum einen jede Fehlerart unterschiedliche Alterungsgeschwindigkeiten zeigt und selbst innerhalb einer Fehlerart bisher sowohl abflachende als auch progressiv steigende Neufehlerzunahmen zum gleichen Thema und in ähnlichen Zeitskalen zu beobachten sind. Da solche Mehrfachmessungen zu einzelnen Themen nur einen kleinen Anlagenbestand zeigen, wären Aussagen hieraus noch nicht tragfähig, weshalb sie, wenn nur als Einzelmessungen dargestellt sind.
Die Glasbrüche zeigen im Verlauf über die Generationen keine besondere Veränderung. Der Ausreiser in der mittleren Generation wird als primär statistische Überhöhung gesehen, da sich 4 der 3 am stärksten betroffenen Anlagen in diesem Zeitabschnitt befinden, die allein etwas über 50% der Glasbrüche stellen.
Die beiden Arten von Substrings im Leerlauf (verursacht durch AD oder LP) zeigen einen kontinuierlichen Trend zur Abnahme. Dieser wird im Kontext einer steigenden Qualität bei der Herstellung der elektrischen Klemm- und Lötverbindungen gesehen.
Die Substrings im Kurzschluss sind um Anlagen mit lokalen Häufungen entsprechend Blitzeinschlägen bereinigt. Die dargestellt übrigen, werden hauptsächlich auf spontanes Versagen der Dioden zurückgeführt, das sich durch bessere Bauteilqualitäten und Auslegungen kontinuierlich gebessert haben kann.
Die unerwartete Steigerung der mangelhaften Anschlussdosen (AD) in der letzten Generation geht mit 2/3 der Gesamtmenge allein auf 2 Anlagen aus 2013 mit einem identischen Anschlussdosentyp zurück und hat daher im zeitlichen Verlauf keine Aussage. Ohne diese Dosen-Thematik ergäbe sich ein leicht fallender Trend.
Die Häufung mangelhaft ausgeführter Lötpunkte (LP) an Quer- und Zellverbinder zeigt, trotz einer flächigen Umstellung auf Lötautomaten, keinen klaren Trend. Die Anzahl betroffener Anlagen mit nur 13 mit je mehr als 5 Mängeln, ist hierfür zu klein.
Die Aufteilung Zellen „erwärmt" mit nicht eindeutiger Ursache und Zellbruch wurde aus der alten Studie übernommen, beide Verläufe zeigen klar, dass die Branche das Thema Zellbruch seit etwa 2012 überwunden hat.
Nach Inbetriebnahme 2013 ist nur noch eine als bedingt relevante bzw. als Empfehlung bewertete PID Anlage aufgefallen. Das Thema ist im Weiteren noch detaillierter aufgeschlüsselt.
2.2.1 Exemplarische Detailbetrachtung PID
Gut 10 % der Anlagen sind von PID betroffen, in denen sich nach Abschätzungen ein aufsummierter Leistungsverlust von 0,5 MW ergab. In vielen Anlagen kam dieser Befund aber erst in den letzten 1-3 Jahren ans Licht, häufig im Rahmen eines Gewährleistungsgutachtens im 5. Betriebsjahr. In der Grafik zeigt sich dies durch die Nähe der Blasen zur diagonalen Linie.
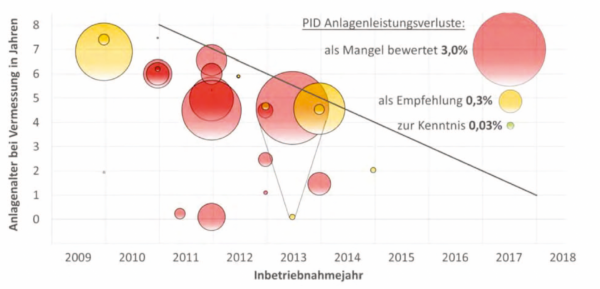
Abbildung 4: Blasendiagramm zur Ausprägung und Abhängigkeit von PI0 bezüglich Inbetriebnahmejahr und Anlagenalter zum Messzeitpunkt. 0ie Farben der Blasen stellen die Bewertung dar, die Größe den abgeschätzten Leistungsverlustanteil in der Anlage durch PID.
Abschätzungen aus Thermogrammen ergaben für eine dieser Anlagen einen Verlust von 3%. In dieser Anlage fand bereits kurz nach der Inbetriebnahme die erste Vermessung statt, wobei noch kein nennenswerter Verlust größer 0,03% abschätzbar war. Die Bewertung erfolgte trotzdem als Empfehlung, da der Verlauf zu höheren Verlusten, ähnlich den dargestellten Verbindungslinien, absehbar war.
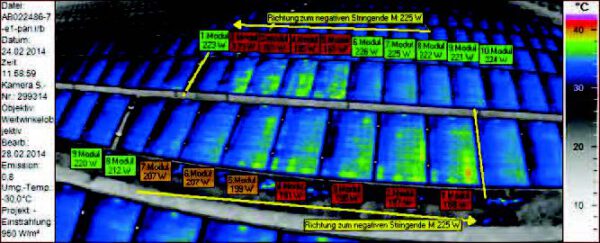
Abbildung 5: Vergleich von Kennlinienmessungen mit den durch PID erwärmten Zellen.
Im Diagramm finden sich auch kleine Blasen mit für die Gesamtanlage unrelevanten Verlusten, aber einer Bewertung als technischer Mangel (rot). In diesen Fällen waren nur vereinzelte Stränge in einer Anlage von PID betroffen, hier allerdings in einer Größenordnung die eine Verletzung der Leistungsgarantie durch einzelne Module erwarten ließ, ähnlich wie im vorangegangenen Thermogramm.
2.2.2 Anteilige Ursachen für Leistungsverluste kristallin
Auch wenn das folgende Ringdiagramm die Relevanz von PID bezüglich Modulfehler in allen Generationen unterstreicht, die maßgelblichen Verluste aus thermografischen Gutachten sind praktisch immer Modulstrings oder Felder im Leerlauf. Die Verluste aller Generationen lagen zwischen 0,80% und 0,93% der Anlagenleistungen, womit Verhältnisse auch absolut weitgehend vergleichbar sind.
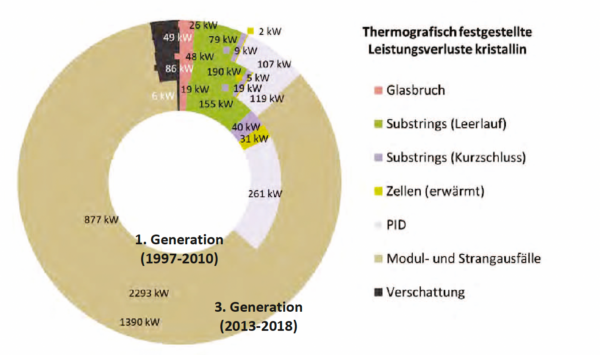
Abbildung 6: Aufgedeckte Leistungsverluste und deren Verhältnisse über die 3 Generationen
Die primäre Aufgabe der PV-Thermografie ist das Auffinden von Defekten auf Modulebene, die durch das Raster der Anlagenüberwachung fallen. Tatsächlich zeigt sich, dass Modulstränge im Leerlauf die dominierenden Gründe für Leistungsverluste sind und diese sich über die 3 Generationen von 0,50% auf 0,78% der Anlagenleistung nennenswert erhöht haben.
Die Ursachen hierfür sind im Gegensatz zur ersten Feldstudie nicht weiter aufgeschlüsselt und auch nicht bei allen Projekten im Detail erfasst worden. Typisch sind, ausgelöste Strangsicherungen, getrennte Stecker, defekte WR und Module.
Die Ursachen hierfür sind im Gegensatz zur ersten Feldstudie nicht weiter aufgeschlüsselt und auch nicht bei allen Projekten im Detail erfasst worden. Typisch sind, ausgelöste Strangsicherungen, getrennte Stecker, defekte WR und Module.
2.2.3 Verbindung zwischen Modulfehlern und Modulstrangausfälle
Ein Teil der Modulstrangausfälle geht auf defekte Module zurück. Bei Dünnschicht- Anlagen ist dies ein recht häufiges Problem. Hierzu kommt es, wenn im Fall von Glasbrüchen eine Zelle weitgehend komplett zerreißt und auch keine Bypassdiode den Stromfluss umleiten kann. Mindestens 15 % der offenen Modulstränge in den Dünnschichtanlagen gehen eindeutig erkennbar auf Glasbrüche zurück, tatsächlich dürfte der Anteil noch deutlich höher liegen.
Bei kristallinen Anlagen ist dieser Zusammenhang schwieriger herzustellen, da hier nicht ähnlich zwingend ein gut erkennbarer Glasbruch vorliegen muss. Im Gegenteil versteckt sich die elektrische Trennung eines Modulstrings häufig, vollständig uneinsehbar in einer äußerlich intakten Anschlussdose. Auch ist es in der gutachterlichen Praxis kaum wirtschaftlich die Ursache für jeden offenen Modulstring im Einzelnen selbst zu klären. Die dann damit beauftragten Installateure und Betriebsführer dokumentieren die Ursachen für Strangausfälle aber meist nicht.
Ohne bisherige statistische Aussagekraft fand sich auch dank Mehrfachmessungen das folgende Schadensbild in mehreren Anlagen:
Bei kristallinen Anlagen ist dieser Zusammenhang schwieriger herzustellen, da hier nicht ähnlich zwingend ein gut erkennbarer Glasbruch vorliegen muss. Im Gegenteil versteckt sich die elektrische Trennung eines Modulstrings häufig, vollständig uneinsehbar in einer äußerlich intakten Anschlussdose. Auch ist es in der gutachterlichen Praxis kaum wirtschaftlich die Ursache für jeden offenen Modulstring im Einzelnen selbst zu klären. Die dann damit beauftragten Installateure und Betriebsführer dokumentieren die Ursachen für Strangausfälle aber meist nicht.
Ohne bisherige statistische Aussagekraft fand sich auch dank Mehrfachmessungen das folgende Schadensbild in mehreren Anlagen:
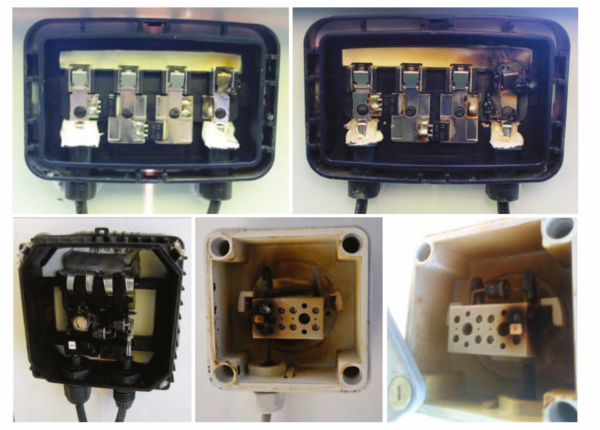
Abbildung 7a-e: Anschlussdosen mit selbstausgelöteten und verlorenen oder defekten Dioden
Die Schadensursache und Folgekette läuft hierbei nach dem folgenden Schema ab:
1. Ein ab Werk unzureichend in der Anschlussdose kontaktiertes Bändchen wird hochohmig, erwärmt dabei häufig über den Schmelzpunkt angrenzender Kunststoffe und verursacht dabei thermische Schäden.
2. In der Regel trennt dieser Kontakt über die Zeit bzw. wird von der Bypass- diode entlastet, die dann im Weiteren meist den vollen Strangstrom trägt.
3. Die Diode und Ihre Kontaktierung wird über die weitere Betriebsdauer von typischerweise mehreren Jahren unter Volllast so weit degradiert, dass sie entweder selbst ausfällt oder an ihren Kontakten trennt. (siehe Bilder zuvor)
4. In diesem Moment trennt die Dose den Modulstring vollständig, wobei die Ursache von außen unerkennbar bleibt.
2. In der Regel trennt dieser Kontakt über die Zeit bzw. wird von der Bypass- diode entlastet, die dann im Weiteren meist den vollen Strangstrom trägt.
3. Die Diode und Ihre Kontaktierung wird über die weitere Betriebsdauer von typischerweise mehreren Jahren unter Volllast so weit degradiert, dass sie entweder selbst ausfällt oder an ihren Kontakten trennt. (siehe Bilder zuvor)
4. In diesem Moment trennt die Dose den Modulstring vollständig, wobei die Ursache von außen unerkennbar bleibt.
Die bisherige Erfahrung mit der Problematik zeigt lediglich, dass Dioden auch über viele Jahre im Dauerbetrieb verbleiben können, ob die Mehrheit der Substrings im Leerlauf mit ihren aktiven Dioden das 20te Lebensjahr erreichen, ist aber fraglich.
2.2.4 Exemplarische Hinweise der Thermografie zur Folienalterung
Wie auch bei den offenen Modulsträngen gibt die Thermografie auch sonst häufig wichtige Hinweise für Themen, für die sie ursprünglich nicht gezielt eingesetzt ist. Das Wichtigste dieser Themen war bisher die Alterung von Modulrückseitenfolien.
Bereits im 2ten Betriebsjahr 2012 ließ sich bei einigen Anlagen mittels Thermografie an Zellbrüchen eine kritische Folienalterung [ZSW] bei mehreren Herstellern erkennen.
Bereits im 2ten Betriebsjahr 2012 ließ sich bei einigen Anlagen mittels Thermografie an Zellbrüchen eine kritische Folienalterung [ZSW] bei mehreren Herstellern erkennen.
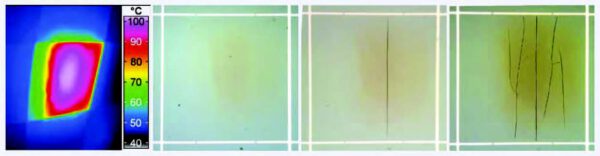
Abbildung 8a-d: Folienalterung aus der Feldstudie 2013 bzw. einem Gutachten aus 2012:
,,Da die Alterungsgeschwindigkeit der Folie aus der Erfahrung als verhältnismäßig hoch ein- geschätzt wird, . empfohlen, die Folie in einem unabhängigen Labor auf Eignung zu prüfen." 0er Zellbruch, die Erwärmung der Zelle in Folge und das Auffinden dieser Zelle mittels Thermografie sind hier nur Hinweisgeber, aber jeweils nicht selbst das relevante Thema.
In den letzten Jahren hat sich, erneut flankiert durch thermografische Messungen, die folgende absehbare Weiterentwicklung dieser Folien gezeigt. Die Degradation der Folie löst die Isolation in der Fläche und den Randverbund auf, wodurch Feuchtigkeit eindringt, was weiter zur Korrosion an Lötpunkten führt:


Abbildung 9a, b: Vorder- und Rückseite desselben Moduls zeigt Korrosion an den Bändchen und lokal thermische Überbelastungen der Folie in Folge hochohmiger, korrodierter Lötpunkte.
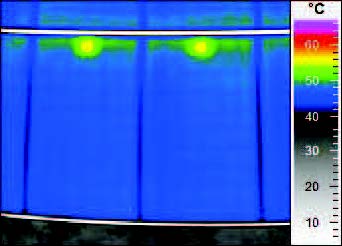
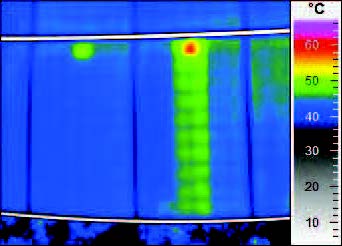
Abbildung 10a und b: Vergleich des Moduls aus den vorangegangenen Bildern in 2017 und 2018: Entstehung eines mittleren Substringfehlers in Folge der Folienalterung. Die Lötpunkte der Querverbinder Bändchen an der Unterkante haben unter zunehmender Korrosion getrennt.
Das letzte Bild zeigt, das Endstadium dieses Fehlers, der üblicherweise als Serienfehler alle Module einer Anlage betrifft, wenn auch in den Modulen in leicht variierender Geschwindigkeit voranschreitet. Das Glas bricht in Folge kleiner Lichtbögen, die als Wackelkontakte an den defekten Lötpunkten zünden. Das Modul fällt, aufgrund fehlender Stabilität durch Glas und Folie, vollständig auseinander:
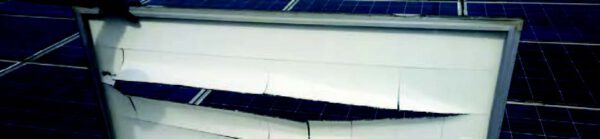
Abbildung 11: 2018 Endstadium eines Moduls mit anfälliger Rückseitenfolie im 8. Betriebsjahr.
23 % der in der Studie untersuchten Module sind potentiell vom Thema betroffen!
2.2.5 Messungen an Dünnschicht Generatoren
Bei der Auswertung der 52 Dünnschichtanlagen mit zusammen 183 MW wurde nicht weiter zwischen den einzelnen enthaltenen Technologien (CdS/CdTe; CIGS; CIS, amorph und Tandem Si) differenziert. Dabei dominierte ein bekannter Hersteller mit CdTe und einem Leistungsanteil von 83%. Für eine zeitliche Aufschlüsselung, wie bei den kristallinen Anlagen, war die Datenbasis nicht groß genug. In der Auswertung zeigten sich mit 0,58% geringere Gesamtverluste als bei kristallinen Anlagen.
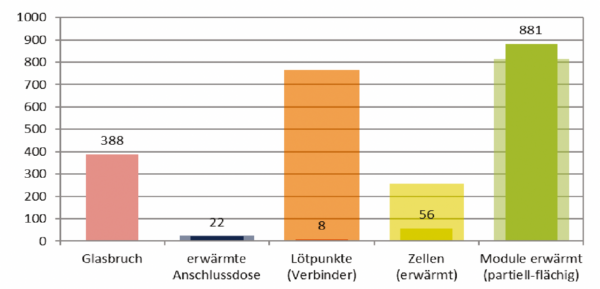
Abbildung 12: Absolute Zahlen Modulmängel Dünnschicht im Vordergrund und Module die als Empfehlung zur langfristigen Beobachtung bewertet wurden ohne Zahl im Hintergrund
Bewertung der Modulmängel und Empfehlungen in Dünnschichtanlagen
Glasglas-DS Module, die den Großteil der vermessenen Module ausmachen, sind konstruktiv bedingt anfälliger für Glasbrüche, womit die hier höheren Zahlen nicht überraschen. Anzumerken ist, dass die Thermografie hier nicht alle Glasbrüche erkennt und entsprechend der größere Teil der Rückseitenglasbrüche im Diagramm fehlt.
Erwärmte Anschlussdosen sind beim gängigsten Modell sehr viel seltener als bei kristallinen Modulen, ggf. da hier kein händischer Prozess zur Verlötung der Kontakte verwendet wird. Versagt dieser Prozess trotzdem ist die Konsequenz in der Regel nach kurzer Zeit ein Glasbruch und ein getrennter Modulstrang.
Nahezu alle DS Module besitzen zwei Lötverbindungen zwischen den Sammelbändchen der jeweils letzten beiden Zellen und dem Querverbinder, der elektrisch kontaktierend auf die Zelle geklebt wird. All diese Verbindungen sind sehr häufig leicht hochohmig was sich typischerweise als Erwärmung um etwa 10 K bei STC zeigt. Während manche DS Modelle bei solchen äußeren Anzeichen bereits zerstört werden, zeigt sich der gängigste Typ dagegen innerhalb der beobachteten, zum Teil 11 Jahre alten Anlagen, stabil. Tatsächlich liegt die Häufung dieser Auffälligkeit bei manchen Anlagen bei über 5%, die aufgeführten Fälle zeigen nur einen sehr kleinen dokumentierten Anteil.
Glasglas-DS Module, die den Großteil der vermessenen Module ausmachen, sind konstruktiv bedingt anfälliger für Glasbrüche, womit die hier höheren Zahlen nicht überraschen. Anzumerken ist, dass die Thermografie hier nicht alle Glasbrüche erkennt und entsprechend der größere Teil der Rückseitenglasbrüche im Diagramm fehlt.
Erwärmte Anschlussdosen sind beim gängigsten Modell sehr viel seltener als bei kristallinen Modulen, ggf. da hier kein händischer Prozess zur Verlötung der Kontakte verwendet wird. Versagt dieser Prozess trotzdem ist die Konsequenz in der Regel nach kurzer Zeit ein Glasbruch und ein getrennter Modulstrang.
Nahezu alle DS Module besitzen zwei Lötverbindungen zwischen den Sammelbändchen der jeweils letzten beiden Zellen und dem Querverbinder, der elektrisch kontaktierend auf die Zelle geklebt wird. All diese Verbindungen sind sehr häufig leicht hochohmig was sich typischerweise als Erwärmung um etwa 10 K bei STC zeigt. Während manche DS Modelle bei solchen äußeren Anzeichen bereits zerstört werden, zeigt sich der gängigste Typ dagegen innerhalb der beobachteten, zum Teil 11 Jahre alten Anlagen, stabil. Tatsächlich liegt die Häufung dieser Auffälligkeit bei manchen Anlagen bei über 5%, die aufgeführten Fälle zeigen nur einen sehr kleinen dokumentierten Anteil.
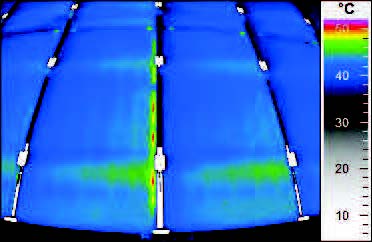
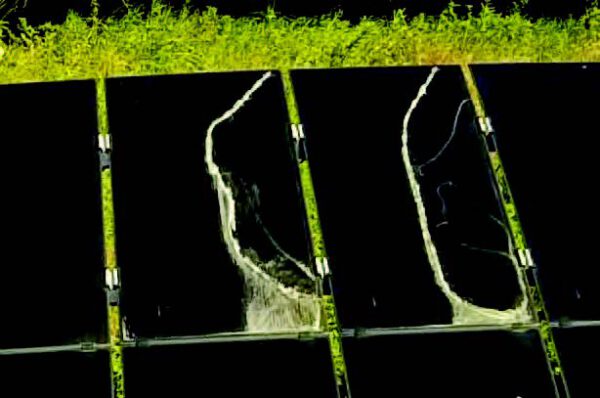
Abbildung 13a und b: Bisher als Sonderfall behandelter Typ eines Dünnschichtmoduls: Hier führten Übergangswiderstände 11%, die ähnlich wie beim gängigen Typ von außen lediglich 10 K Temperaturüberhöhung an den Bändchen-Übergängen zeigen, bereits nach 4 Betriebsjahren zu 3% Glasbrüchen mit absehbar steigender Tendenz. Da das Gutachten auf eine Detailklärung angelegt, die Problematik aber bereits bekannt war, sind diese Module nicht in der Statistik.
Auch in DS Modulen finden sich erwärmte Zellen, auch wenn diese selten eindeutig als Einzelzellen identifizierbar sind, da die abschirmende Glasdicke das thermische Profil ungerichtet zerstreut. Die Bewertung dieser und flächig erwärmter Module, wie sie auch so genannte „Low Power" Module zeigen, erfolgt ohnehin über flächigere Temperaturmessungen. Die Thermografie ist allerdings hier aktuell wirtschaftlich nur in der Lage die Module mit den deutlichsten Verlusten anzuzeigen.
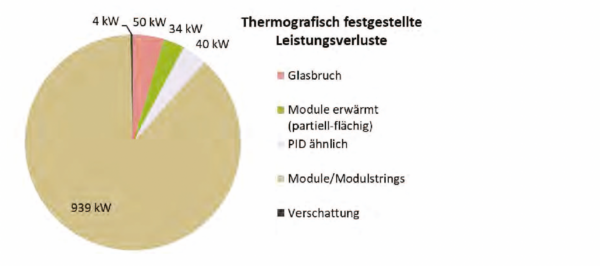
Abbildung 14: Nur Glasbrüche und flächige erwärmte Module verursachen Verluste, den größten Teil machen, insbesondere bei 0S unerkannt, ausgefallene Modulstrings aus.
In DS-Anlagen ersetzt die Thermografie teils hochaufgelöste Strangüberwachungen.
2.3 Auffälligkeiten in elektrischen B0S Komponenten
Die BOS Komponenten aus den 962 MW der untersuchten Anlagen waren bei Messungen in der Regel nach den beiden Hauptgruppen aufgeteilt.
- GAKs oder ACHVs;
- Zentral- oder String- WR;
- Zentral- oder String- WR;
Mittlere Stichprobe 23% => 221 MW
Mittlere Stichprobe 17% => 164 MW
Mittlere Stichprobe 17% => 164 MW
DCHVs werden dabei zum Zentral-WR hinzugezählt, da sie in diese ohnehin oft integriert oder direkt davor aufgestellt sind. Anlagenkonzepte mit Zentral-WR machten mit 632 MW, 2/3 der Gesamtleistung aus. In den meist als Stichproben vermessenen Anlagen war die Aufteilung vergleichbar.
Die folgende Darstellung unterteilt zum einen nach den drei Elementen:
Die folgende Darstellung unterteilt zum einen nach den drei Elementen:
- Komponenten: Bauteile wie Schalter, Sicherungen, Messertrenner, usw.
- Abgänge: Vor-Ort konfektionierte und oder aufgelegte Kabelabgänge beispielsweise zwischen Modulstring und GAK oder GAK und WR
- Verbinder: Vorkonfektionierte Verbindungen innerhalb der Hauptgruppen
- Abgänge: Vor-Ort konfektionierte und oder aufgelegte Kabelabgänge beispielsweise zwischen Modulstring und GAK oder GAK und WR
- Verbinder: Vorkonfektionierte Verbindungen innerhalb der Hauptgruppen
Diese Gruppen sind Ihrerseits in DC und AC Bereiche aufgeteilt, wobei die Einzelbefunde sortiert nach den 3 relevanten Bewertungsgruppen aufgeführt sind.
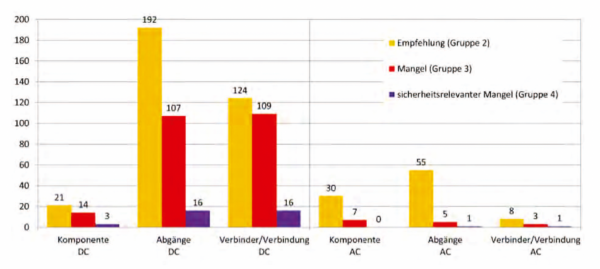
Abbildung 15: Die in Summe 712 Auffälligkeiten innerhalb der aufgeführten Bauteile mit zusammen 385 MW ergibt pro MW knapp 2 Auffälligkeiten.
Auffallend ist die geringere Anzahl von Auffälligkeiten im AC Bereich. Aus Aufwandsgründen war es bisher nicht möglich diese ins Verhältnis zu den untersuchten Komponenten und Verbindungszahlen im jeweiligen Bereich zu stellen. Da aber mehrere auch Kleinserienfehler im DC- im Gegensatz zum AC-Bereich bekannt sind, kann davon ausgegangen werden, dass hier die Problematik der Materialpaarung bzw. elektrochemische Korrosion im DC Bereich eine Rolle spielt.Bei 37 Auffälligkeiten erfolgte eine Bewertung als sicherheitsrelevanter Mangel was häufig eine direkte Abschaltung in Abstimmung mit dem Betreiber im Sinne des Brandschutzes zur Folge hatte. Zwei Beispiele im Folgenden für je eine fehlerhafte Crimpung und eine V-Klemme.
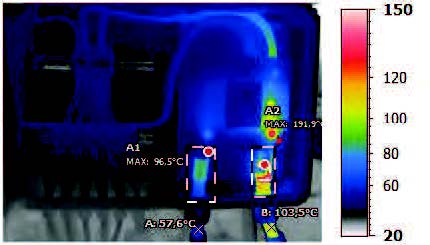
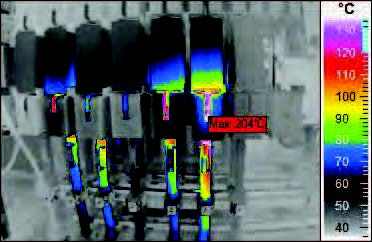
Abbildung 16a und b: Die Thermogramme zeigen je einen gecrimpten Abgang in einem GAK unter einem Leistungsschalter (links) und einen Abgang kontaktiert über eine V-Klemme unter einer NH-Sicherung in einem WR (r): Beide zeigen Temperaturen um 200°C und damit über dem Schmelzpunkt mancher Isolierstoffe. Beide Kontakte wurden aufgrund der akuten Brandgefahr direkt nach Aufnahme des Befunds außer Betrieb genommen bzw. entlastet. Auch wenn es in diesen Fällen noch nicht zu einem Brand gekommen ist, können angrenzende Bauteile wie ein Leistungsschalter durch die thermische Belastung bereits beschädigt worden sein.
Der problematischste Befund in der PV-Elektro-Thermografie ist allerdings nicht die Häufung von knapp 2 Auffälligkeiten pro MW, sondern der Umgang mit Befunden, insbesondere nach Abbränden. In deutschen Freiflächenanlagen sind Schäden zwar in der Regel im schlimmsten Fall auf den Abbrand eines GAK beschränkt oder enden sogar mit dem Abbrand einer Klemme.
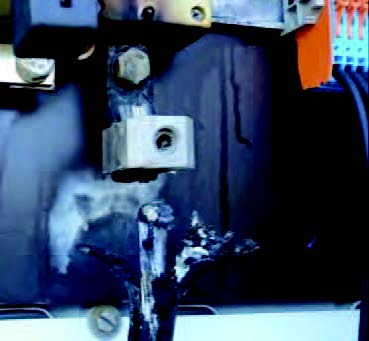
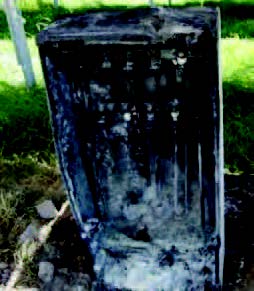
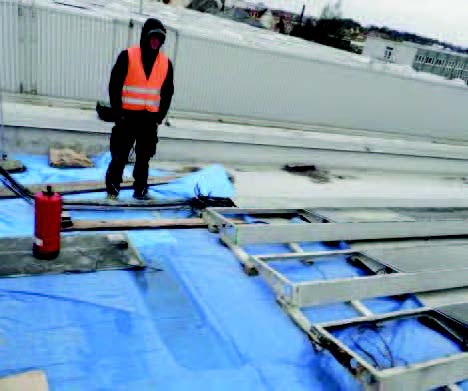
Abbildung 17a: Lokaler Abbrand einer DC-Schalter-Hauptklemme
b: Ausgebrannter DC-Hauptsammler auf einer Freiflächenanlage;
c: Lokaler Durchbrand eines Foliendachs entlang zweier DC-Hauptkabel als Folge eines Kurzschlusses und eines wandernden Lichtbogens.
b: Ausgebrannter DC-Hauptsammler auf einer Freiflächenanlage;
c: Lokaler Durchbrand eines Foliendachs entlang zweier DC-Hauptkabel als Folge eines Kurzschlusses und eines wandernden Lichtbogens.
Auf Dächern und insbesondere auf Foliendächern mit verminderter Brandhemmung im Vergleich zu harten Deckungen, ist dagegen sowohl eine ordentliche Analyse als auch eine entsprechende Korrektur im Nachgang unerlässlich.Die Erfahrung zeigt leider, dass dem nicht immer Rechnung getragen wird. So ist es kaum nachvollziehbar, wie nach einem Abbrand auf einem Dach und nach einem großflächigen Umbau, erneut langfristig problematische Konstruktionen und Ausführungen installiert werden können, wie in den folgenden Beispielen zu sehen.
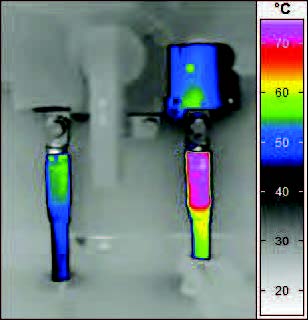
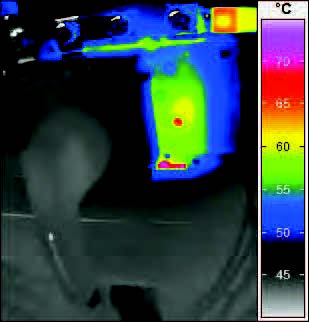
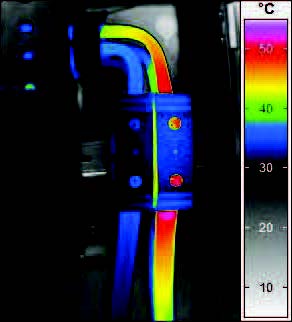
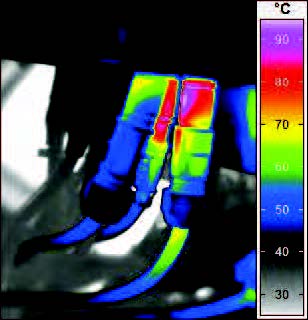
Abbildung 18a-d: Kritische Übergangswiderstände an Hauptabgängen von GAKs: Die 4 GAK-Thermogramme eint, dass sie in 3 Fällen nach einem Brandfall und NACH einer, zum Teil aufwändigen, aber erfolglosen Reparatur in MW-Anlagen, thermografiert wurden.
Über die Ursachen kann an dieser Stelle nur spekuliert werden. Neben der bereits angesprochenen Problematik von DC-Strom, insbesondere in Kombination mit häufig verwendeten Alu-Hauptleitungen, kann weiter eine Rolle spielen, dass eine ausreichende Kabelreserve häufig nicht angelegt ist.
Entsprechend kann ein Installateur vor der Wahl stehen einen abgebrannten Hauptabgang aufwändig auszugraben, zu verlängern und ordentlich neu aufzulegen, oder das verbleibende zu kurze Stück unter mechanischer Spannung, zu kurz abgeschnitten und auf einem noch oberflächenkorrodierten Ende neu aufzulegen.
Wenn dann auch noch das Geld für eine Nachprüfung der Instandsetzung beispiels- weise mittels Thermografie eingespart wird, bleibt nur die Hoffnung, dass es hält.
Entsprechend kann ein Installateur vor der Wahl stehen einen abgebrannten Hauptabgang aufwändig auszugraben, zu verlängern und ordentlich neu aufzulegen, oder das verbleibende zu kurze Stück unter mechanischer Spannung, zu kurz abgeschnitten und auf einem noch oberflächenkorrodierten Ende neu aufzulegen.
Wenn dann auch noch das Geld für eine Nachprüfung der Instandsetzung beispiels- weise mittels Thermografie eingespart wird, bleibt nur die Hoffnung, dass es hält.
2.3.1 Grenzen der PV-El-Thermografie
Die meisten PV-elektro-thermografischen Befunde sind Übergangswiderstände, häufig an im Freien konfektionierten Verbindern, die gut mittels Thermografie erfasst werden können. Es sind allerdings aus vielen Gesprächen mit Betriebsführern einige Situationen und Bauteile bekannt, deren Ausfall sich nicht rechtzeitig thermisch ankündigen, hierzu zählen beispielsweise.
- Einzelne Modelle von DC-Strangsicherung
- Einzelne IGBTs in ZWR
- Einzelne IGBTs in ZWR
Auch ist in der Praxis bereits die Prüfung bestimmter Komponenten, trotz Aussicht auf einen Befund, rein wirtschaftlich schwierig. Hierzu zählen z.B.: einzelne ZWR Modelle, bei denen ein Entblechen bzw. das Entfernen von Abdeckungen in keinem Verhältnis zu den hierüber einsehbaren möglichen Befunden steht.
3. Wirtschaftlichkeit der Thermografie
Die Studie soll auch eine Basis sein, die Eignung und Wirtschaftlichkeit der thermografischen PVA Prüfung im einzelnen Projektfall einzuschätzen. Diese wird maßgeblich von den folgenden Faktoren beeinflusst:
- Größe der Anlage und ggf. Stichprobe
- Inbetriebnahme Datum, Anlagenalter und Strompreis,
- Anzahl der erwartbaren Fehler und deren direkte Betriebsbeeinträchtigungen
mögliche vermeidbare Folgeschäden bis zum Brandschutz
- Bewertung weiterer Hinweise aus thermografischen Untersuchungen
- Inbetriebnahme Datum, Anlagenalter und Strompreis,
- Anzahl der erwartbaren Fehler und deren direkte Betriebsbeeinträchtigungen
mögliche vermeidbare Folgeschäden bis zum Brandschutz
- Bewertung weiterer Hinweise aus thermografischen Untersuchungen
Eine wirtschaftliche Vermessung von Anlagen unter 100 kW ist aus der Erfahrung auch bei Anlagen mittleren Alters meist schwierig. Da entsprechend wenige Vermessungen aus diesem Bereich zur Verfügung stehen, sind diese auch in der Feldstudie nicht weiter berücksichtigt.⁸ Die Anzahl der erwartbaren Fehler und deren Verluste sind in den vorangegangenen Kapiteln dargestellt.
Die Vermessung der neuesten Ausschreibungsanlagen mit Vergütungssätzen zwischen 4-5 ct/kWh oder rein kommerzielle Projekte mit ca. 3 ct/kWh sind auch für die Thermografie Herausforderungen im Vergleich zu Anlagen mit 21 ct/kWh aus 2011. Diese Herausforderungen bleiben aber dank erheblicher Effizienzsteigerungen und Kostensenkung in der Vermessung beherrschbar. Selbst für zuletzt genannte rein kommerzielle Projekte besteht Interesse an thermografischen Untersuchungen.
Noch relevanter als die im Folgenden dargestellte Vermessungsleistung an PV- Generator und BOS Komponenten ist die Auswertungsgeschwindigkeit, aber auch hier gibt es zum einen den Trend KI zur Mustererkennung einzusetzen und zusätzlich werden in Zukunft ggf. auch weniger Komponenten als wirtschaftlich austauschbar gelten, weswegen auch deren Auswertung im Einzelnen weniger relevant werden kann. Das Interesse um das Wissen über potentiell gravierende Serienfehler wie die dargestellte Folienalterung bei kristallinen Modulen, Glasbrüchen durch Übergangswiderstände bei Dünnschicht oder an DC-Abgängen der BOS-Komponenten, dürfte davon unabhängig sein. Nicht jedes Modul mit Serienfehler muss persönlich mit Seriennummer lokalisiert werden, um einen Serienfehler nachzuweisen. Oft reicht ein Nachweis der Häufung wie beim Folienthema um einen durch viele Hersteller bereits laufenden Komplettaustausch von Anlagen zu veranlassen.
Die Vermessung der neuesten Ausschreibungsanlagen mit Vergütungssätzen zwischen 4-5 ct/kWh oder rein kommerzielle Projekte mit ca. 3 ct/kWh sind auch für die Thermografie Herausforderungen im Vergleich zu Anlagen mit 21 ct/kWh aus 2011. Diese Herausforderungen bleiben aber dank erheblicher Effizienzsteigerungen und Kostensenkung in der Vermessung beherrschbar. Selbst für zuletzt genannte rein kommerzielle Projekte besteht Interesse an thermografischen Untersuchungen.
Noch relevanter als die im Folgenden dargestellte Vermessungsleistung an PV- Generator und BOS Komponenten ist die Auswertungsgeschwindigkeit, aber auch hier gibt es zum einen den Trend KI zur Mustererkennung einzusetzen und zusätzlich werden in Zukunft ggf. auch weniger Komponenten als wirtschaftlich austauschbar gelten, weswegen auch deren Auswertung im Einzelnen weniger relevant werden kann. Das Interesse um das Wissen über potentiell gravierende Serienfehler wie die dargestellte Folienalterung bei kristallinen Modulen, Glasbrüchen durch Übergangswiderstände bei Dünnschicht oder an DC-Abgängen der BOS-Komponenten, dürfte davon unabhängig sein. Nicht jedes Modul mit Serienfehler muss persönlich mit Seriennummer lokalisiert werden, um einen Serienfehler nachzuweisen. Oft reicht ein Nachweis der Häufung wie beim Folienthema um einen durch viele Hersteller bereits laufenden Komplettaustausch von Anlagen zu veranlassen.
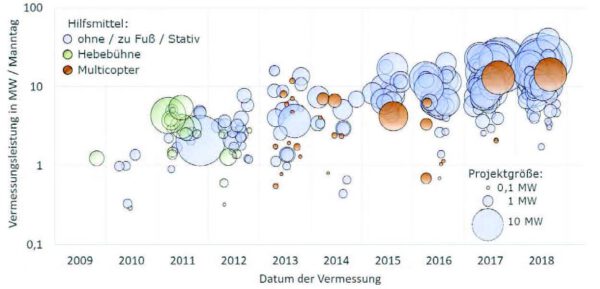
Abbildung 19: Deutliche Lernkurve bei der Vermessung des PV-Generators / Module; Die Vermessungsleistung vor knapp 10 Jahren lag bei 1-2 MW im Vergleich zu heute bei 10-20 MW.
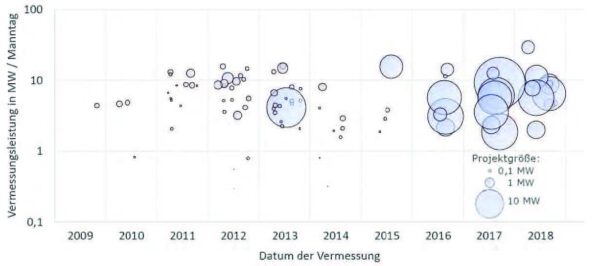
Abbildung 20: Die Darstellung zeigt ein steigendes Interesse für größere Stichproben zur Elektro-Thermografie in letzter Zeit, trotz einer scheinbar geringen Messbeschleunigung; Die Vermessungen über die Jahre sind in Ihrer Vermessungsleistung weniger vergleichbar als beim PV-Generator. Während das Wissen um die Notwendigkeit von Ausblecharbeiten (Entfernen von Plexiglas) um 2010 noch gering war und nur zu etwa 10% durchgeführt wurde, liegt der Ausblech-Anteil heute in der Größenordnung von 80%. 0ie hierzu erforderlichen erheblichen Arbeitszeiten sind in die Grafik zur reinen Messzeit addiert. Als Faktor liegen sie typischerweise zwischen 1x (kein Aufwand) und 5x bzw. im Mittel bei etwa 3x. Entsprechend fehlt dieser Faktor 3 auch in der Steigung der Lernkurve. Dieser Faktor 3 wurde über die Jahre also in die Qualitätssteigerung der Messung und nicht in deren Beschleunigung investiert.
4. Ergebnisse der Feldstudie 2.0
Bei kristallinen Anlagen hat sich der Anteil als mangelhaft bewerteter Module von knapp 0,6%, in der ersten Generation (bis 2010), auf knapp 0,3%, in der letzten Generation (ab 2013), halbiert. Einzelne Probleme sind praktisch gänzlich aus neuen Installationen verschwunden, wie Zellbrüche bis ca. 2011 und PID bis 2014.
Die thermografisch erkennbaren Gesamtverluste in Anlagen, inkl. Modulschäden, sind bei kristallinen Anlagen über alle drei Generationen von 0,80% auf 0,93% aber leicht gestiegen. Der Grund hierfür ist, dass sich der Anteil der Verluste auf Strangebene von 0,50% auf 0,78% deutlich erhöht hat. Dünnschichtanlagen zeigten dagegen kleinere Gesamtverluste mit 0,58% und der Anteil an Strangausfällen lag ähnlich denen kristalliner Anlagen der ersten Generation bei 0,51 %.
Die Ursache der Strangausfälle konnte die Studie nicht bestimmen. In der ersten Feldstudie lagen Verluste auf Strangebene noch bei 1,4% der Anlagenleistung. Grund für diesen damals höheren Wert kann der deutlich höhere Prüfanteil zu Abnahmen direkt nach Inbetriebsetzung sein. Die drei wichtigsten damalig folgendermaßen aufgeschlüsselten Gründe lagen bei 0,46% aus Installationsfehlern so wie WR und Sicherungsausfällen (0,56% + 0,15%) die einen relevanten Anteil Kinderkrankheiten aus den ersten Betriebsmonaten darstellen dürften.
Ein verbleibender bzw. perspektivisch über die Jahre ansteigender Grund für Strangausfälle sind Modulfehler. Dieser Anteil ist aber nur schwer erfassbar, zumindest für Dünnschicht konnte ein Anteil von mindestens 15% durch Glasbrüche nachgewiesen, der aber tatsächlich noch deutlich höher liegen dürfte. Erfahrungen aus Einzeluntersuchungen lassen vermuten, dass nicht alle der Bypassdioden, die heute defekte Module überbrücken 20 Jahre unter Volllast überstehen werden. Mehrfachmessungen zeigen aber, dass dies zumindest über mehrere Betriebsjahre für die Mehrzahl der Dioden möglich ist. Da die Prognose dieser Ausfälle und damit der Relevanz von Modulfehlern für den Betrieb alternder Anlagen wichtig werden kann, sollten die Lebensdauer bzw. Ausfälle von Dioden in Zukunft im Blick bleiben.
Aus den Daten der Elektro-Thermografie zeigt sich, dass sich pro MW knapp 2 relevante Auffälligkeiten finden. Bei gleichzeitiger Untersuchung von GAKs und WR ergäben sich knapp 4 Auffälligkeiten⁹, wovon mindestens eine als technischer Mangel bewertet wäre. Weiter zeigt die Erfahrung aus Nachkontrollen, dass ein Einbinden der Thermografie sowohl durch interne als auch externe, Kräfte ein wichtiges Mittel sein kann Probleme nicht nur frühzeitig zu erkennen, sondern auch eine zuverlässige Instandsetzung zu gewährleisten.
Die Ursache der Strangausfälle konnte die Studie nicht bestimmen. In der ersten Feldstudie lagen Verluste auf Strangebene noch bei 1,4% der Anlagenleistung. Grund für diesen damals höheren Wert kann der deutlich höhere Prüfanteil zu Abnahmen direkt nach Inbetriebsetzung sein. Die drei wichtigsten damalig folgendermaßen aufgeschlüsselten Gründe lagen bei 0,46% aus Installationsfehlern so wie WR und Sicherungsausfällen (0,56% + 0,15%) die einen relevanten Anteil Kinderkrankheiten aus den ersten Betriebsmonaten darstellen dürften.
Ein verbleibender bzw. perspektivisch über die Jahre ansteigender Grund für Strangausfälle sind Modulfehler. Dieser Anteil ist aber nur schwer erfassbar, zumindest für Dünnschicht konnte ein Anteil von mindestens 15% durch Glasbrüche nachgewiesen, der aber tatsächlich noch deutlich höher liegen dürfte. Erfahrungen aus Einzeluntersuchungen lassen vermuten, dass nicht alle der Bypassdioden, die heute defekte Module überbrücken 20 Jahre unter Volllast überstehen werden. Mehrfachmessungen zeigen aber, dass dies zumindest über mehrere Betriebsjahre für die Mehrzahl der Dioden möglich ist. Da die Prognose dieser Ausfälle und damit der Relevanz von Modulfehlern für den Betrieb alternder Anlagen wichtig werden kann, sollten die Lebensdauer bzw. Ausfälle von Dioden in Zukunft im Blick bleiben.
Aus den Daten der Elektro-Thermografie zeigt sich, dass sich pro MW knapp 2 relevante Auffälligkeiten finden. Bei gleichzeitiger Untersuchung von GAKs und WR ergäben sich knapp 4 Auffälligkeiten⁹, wovon mindestens eine als technischer Mangel bewertet wäre. Weiter zeigt die Erfahrung aus Nachkontrollen, dass ein Einbinden der Thermografie sowohl durch interne als auch externe, Kräfte ein wichtiges Mittel sein kann Probleme nicht nur frühzeitig zu erkennen, sondern auch eine zuverlässige Instandsetzung zu gewährleisten.
5. Ausblick Feldstudie 3.0
Die vorliegende Feldstudie 2.0 ist eine in vielen Teilen stark kondensierte und vereinfachte Darstellung, der in den Daten enthaltenen Informationen. Bereits ausgehend von der ersten Feldstudie wurden viele weitere Aspekte noch im Nachgang und auch meist nicht öffentlich ausgewertet. Ein wichtiger Teil hierbei waren die Auswertung für mehrere Großkunden und deren Anlagen. Dies diente den Betriebsführern und Betreibern zur Priorisierung der für ihren Anlagenbestand notwendigen weiteren Bearbeitungsschritte. Ähnlich wie diese kleinen Teilfeldstudien
„1.x" sollen auch aus dem jetzigen Datenbestand noch weitere öffentliche und nicht öffentliche Feldstudien 2.x erarbeitet werden.
Langfristiges Ziel ist es in ein paar Jahren eine erneute Gesamtschau in Form einer Version 3.0 zu veröffentlichen. Hierzu wird auch in Erwägung gezogen Daten von anderen weltweit agierenden PV-Thermografen mit ähnlich umfangreichen Datenbeständen hinzu zu ziehen, die zum Teil auch bereits in verkürzter Form veröffentlicht wurden. Die Herausforderung wird hierbei sein, eine gemeinsame vergleichbare Qualitätsbasis zu finden, die im besten Fall der IEC TS 62446-3 entspricht.
Langfristiges Ziel ist es in ein paar Jahren eine erneute Gesamtschau in Form einer Version 3.0 zu veröffentlichen. Hierzu wird auch in Erwägung gezogen Daten von anderen weltweit agierenden PV-Thermografen mit ähnlich umfangreichen Datenbeständen hinzu zu ziehen, die zum Teil auch bereits in verkürzter Form veröffentlicht wurden. Die Herausforderung wird hierbei sein, eine gemeinsame vergleichbare Qualitätsbasis zu finden, die im besten Fall der IEC TS 62446-3 entspricht.
6. Quellen
[ISE1] Bruno Burger, https://www.energy-charts.de/index_de.htm Fraunhofer ISE, Freiburg 21.Feb. 2019
[SolS] B. Weinreich; Solarschmiede GmbH; Feldstudie zur Modul- und Generatorqualität auf Basis thermografischer Messungen über 100 MW, 28.PV-Symposium, Bad Staffelstein 2013
[ISE2] H. Wirth, Aktuelle Fakten zur Photovoltaik in Deutschland, Fraunhofer ISE, Freiburg 18.Feb. 2019
[IEC] TS 62446-3 Edition 1.0 2017-06: Photovoltaic (PV) systems - Requirements for testing, documentation and maintenance - Part 3: Photovoltaic modules and plants - Outdoor infrared thermography
[ZSW] P. Lechner; Zentrum für Sonnenenergie- und Wasserstoff-Forschung Baden- Württemberg, Bewertung von Auffälligkeiten und Schäden an der Rückseitenfolie von PV- Modulen, 34.PV-Symposium, Bad Staffelstein 2019 [0KE] DIN VDE V 0126-23-3 (Ed. 2: April 2018) Photovoltaik (PV)-Systeme - Anforderungen an Prüfung, Dokumentation und Instandhaltung - Teil 3: Photovoltaische Module und Betriebsanlagen - Infrarot-Thermografie im Freien
[SolS] B. Weinreich; Solarschmiede GmbH; Feldstudie zur Modul- und Generatorqualität auf Basis thermografischer Messungen über 100 MW, 28.PV-Symposium, Bad Staffelstein 2013
[ISE2] H. Wirth, Aktuelle Fakten zur Photovoltaik in Deutschland, Fraunhofer ISE, Freiburg 18.Feb. 2019
[IEC] TS 62446-3 Edition 1.0 2017-06: Photovoltaic (PV) systems - Requirements for testing, documentation and maintenance - Part 3: Photovoltaic modules and plants - Outdoor infrared thermography
[ZSW] P. Lechner; Zentrum für Sonnenenergie- und Wasserstoff-Forschung Baden- Württemberg, Bewertung von Auffälligkeiten und Schäden an der Rückseitenfolie von PV- Modulen, 34.PV-Symposium, Bad Staffelstein 2019 [0KE] DIN VDE V 0126-23-3 (Ed. 2: April 2018) Photovoltaik (PV)-Systeme - Anforderungen an Prüfung, Dokumentation und Instandhaltung - Teil 3: Photovoltaische Module und Betriebsanlagen - Infrarot-Thermografie im Freien
¹ GAKs, ACHVs: DC - Generatoranschlusskästen / AC - Hauptverteiler
² IEC-Norm: ".Photovoltaic modules and plants - Outdoor infrared thermography"
³ BOS = Balance of System = Alle Komponenten einer PV-Anlage außer den Modulen
⁴ Mismatch = elektrische Ungleichgewichte im PV-Generator, die sich in einer Generator-Kennlinie als Knicke darstellen und entweder durch Planungsfehler oder äußere Umstände wie lokale Verschattungen oder Defekte verursacht werden können
⁵ Deutsche Version der IEC Norm zur PV-Thermografie
⁶ VATh-Richtlinie Elektrothermografie, Teil B: Niederspannung; ausgegeben vom deutschen Bundesverband für angewandte Thermografie e.V. (VATh)
⁷ DIN 54191:2017-10, Zerstörungsfreie Prüfung - Thermografische Prüfung elektrischer Anlagen
⁸ Anmerkung: Für Anlagen unter 100 kW wird zumindest eine vereinfachte Thermografie-Inbetrieb- nahmeprüfung durch den Errichter empfohlen, wie sie auch in der IEC TS 62446-3 vorgesehen ist.
⁹ 4 Auffälligkeiten, davon ausgehend, dass diese auf WR und GAK weitgehend gleich verteilt sind, was bisher nicht im Detail untersucht wurde.
² IEC-Norm: ".Photovoltaic modules and plants - Outdoor infrared thermography"
³ BOS = Balance of System = Alle Komponenten einer PV-Anlage außer den Modulen
⁴ Mismatch = elektrische Ungleichgewichte im PV-Generator, die sich in einer Generator-Kennlinie als Knicke darstellen und entweder durch Planungsfehler oder äußere Umstände wie lokale Verschattungen oder Defekte verursacht werden können
⁵ Deutsche Version der IEC Norm zur PV-Thermografie
⁶ VATh-Richtlinie Elektrothermografie, Teil B: Niederspannung; ausgegeben vom deutschen Bundesverband für angewandte Thermografie e.V. (VATh)
⁷ DIN 54191:2017-10, Zerstörungsfreie Prüfung - Thermografische Prüfung elektrischer Anlagen
⁸ Anmerkung: Für Anlagen unter 100 kW wird zumindest eine vereinfachte Thermografie-Inbetrieb- nahmeprüfung durch den Errichter empfohlen, wie sie auch in der IEC TS 62446-3 vorgesehen ist.
⁹ 4 Auffälligkeiten, davon ausgehend, dass diese auf WR und GAK weitgehend gleich verteilt sind, was bisher nicht im Detail untersucht wurde.